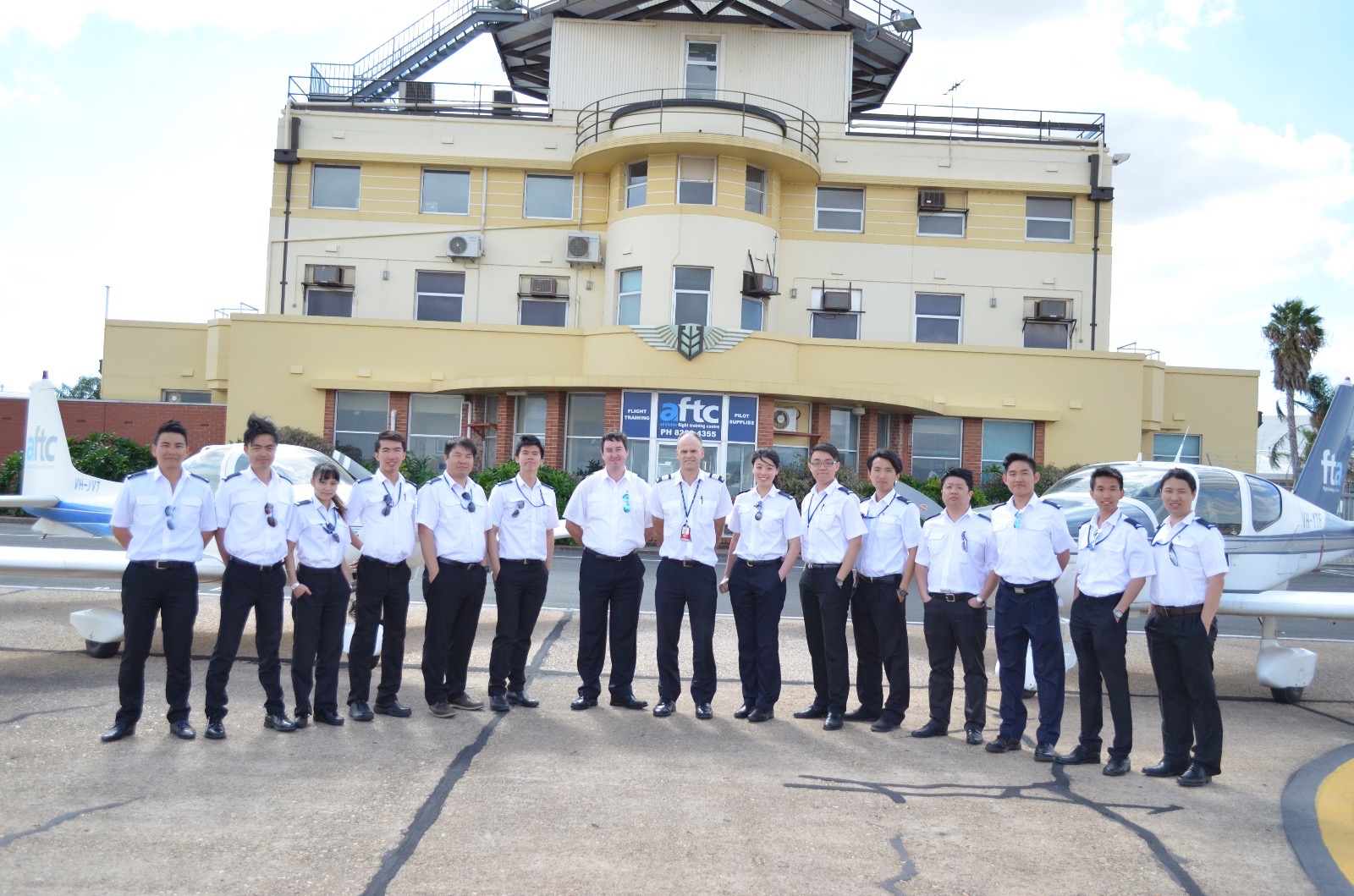
AFTC Training Sharing – Operation
2016/04/11
Today, it is the first day I come back to Hong Kong from the Adelaide via the Singapore. Although I have set the first clock on 0650, I wake up at 0720 at the end. I am not sure if my mum turn the first alarm off. What I want to share is that it is better (have to) prepare more than one clock – use two different brand or at least two model of clock – setting multi-alarm in one device is not work if the time zone has changed – this is what I learned in the trip at AFTC. I do remember that my clock was faster than the local mean time at the date of 3rd April, 2016. I always believe that experience is helpful in my growing. Before I went to the Adelaide, Calvin, who is my ground school tutor, had been telling us about the time of difference between summer and winter. Yet, I had not noticed the LOC has changed from summer time (UTC +10.5) to winter time (UTC +9.5) until I and my group mates were waiting for the table of a restaurant in Glenelg.
After one day working, I can have time to type the diary again. Rightly, I want to type as much as I experienced in the training. Today, let me share about the operation as a starting.
I waked up around 0530 LOC everyday. After a fast grooming (ie. brush my teeth, wash my face, change from home dressing to the pilot uniform. Then, I checked the weather from Bom (Bureau of Meteorology) – I read the Aviation Weather Packages, Area Forecasts (ARFOR) [Area 50] and TAF (Aerodrome Forecasts). I also did some revision about the Mass briefing materials. Around 0700, I and group mates had breakfast in the Mess. After that, we went to the “classroom” at the first floor of the YPPF tower. The instructors did a quick revision for us and told us about the accuracy of that day maneuver(s), but they always remind us – don’t trace the performance.
I had been arranged various slot time from the first flight at around 0815 to 1200 and the last flight at 1500. At the first day, I did not know where I can take the weight & balance sheet (load sheet) nor the performance calculation sheets for T/O and LDG. After the first flight with Dean, one of my respectful instructor, I did it every day before half an hour of the slot time – not too close nor too preceding it – the reason is simply: I don’t like to be rush while I want to use the most current ATIS (Automatic Terminal Information Service) in calculation. Also, I took the Hi-vis Vest, the headset and cushions.
After I met my instructor, I entered the SAR time into the computer system. The SAR time is usually 2.5 hours later of the starting slot time. Then there were two working flow appeared – going to the OPS room inside the Hanger 54 or base of tower, but both also had to do the pre-flight inspection.
In the case that going to Hanger 54, I needed to do few more steps – tear the last carbon copy of Part 2 in the Maintenance Release (MR) and placed that on specific tray, that classified by aircraft model. I also needed to take the key from the cupboard and filled the key-out record.
Instructors may swap the sequence between external check and electrical check. However, the detail is same:- in the training, Dean only care about if there is any missing. Okay, let me recall the memory about what I did in the 10 flights.
I have to declare at this moment – all the information below only can be used as reference. I am sharing my experience. If you want to clarify the knowledge, please consult to your instructor.
Airframe External Inspection
- Open both gull-wing door
the locking status please refer to the label just beneath the latch, that can be rotated - Enter the cockpit
Be careful! We ONLY can step on the area with a black lamination (your instructor must demonstrate to you) - Remove the control lock
Pull out vertically – and place that at a pocket on the L.H.S of the center pedestal - Fill the control wheel status
rotate left and right, it should be free to move. - Magneto – OFF position
- All electronic switch – OFF position
- Main Switch – ON
- Fuel gauge – read the reading
- Flaps – full down (LDG Position)
Lower the flaps stage-by-stage - Fuel drain tube – take from the pocket at the back of L.H seatTo prevent the door closed (slammed) due to strong wind – remember closing it before leaving the cockpit
- Flaps – should be secured
remember check the actuator as well (with the red line) - Move the L.H.S aileron
the control wheel inside the cockpit should be rotate to left if deflect the aileron upward
(so the control wheel should rotate to the right if deflect the aileron downward) - Wing tip
Light cover should be intact;
use hand to push the wing upward as well - Leading edge
Pull and rotate the latch of the tank cap – visual check the quantity - Remove the tie down rope
- Check the stall warning device – no obstruction
- Remove pitot tube cover – check no obstruction
- Light cover – intact
(P.s LDG light on the outer position – more near the wing tip) - Drain the fuel – check no water contamination, no rust, color code – green (Grade 100) in FTA
(p.S the fuel was looking like a pale blue color – but it is green) - Check the fuel vent – no obstruction
- L.H.S Undercarriage
Tyre pressure, two groove, no fluid leakage and fairing intact - Wind shield – clean
in case of needing clean – immerse the spongy into bucket of water and then squeeze all the water off , wipe the window from up to down. - Cowling intact
Sticker with bird mean that had bird strike before - L.H.S air intake x2
one is related to the ventilation sys
another is related to the engine - Propeller – no nick
- Spinner / Propeller cone – intact, secured
- Nose wheel
Tyre pressure, two groove, no fluid leakage and fairing intact - R.H.S air intake for ventilation System
- R.H.S landing gear
Tyre pressure, two groove, no fluid leakage and fairing intact - R.H.S leading edge
Fuel drain + Strainer;
pour the drained fuel on the side of the fence (concrete surface)
or pour into the white bucket - R.H.S Wing tip
- R.H.S Trailing edge
- R.H.S Rear Empennage
remove static source cover – no obstruction;
windows – clean - Vertical stabilizer – shake it
- Trim device – check
by move the stabilator upward;
the condition of hinge and connection - L.H.S Rear Empennae
put all rope and pitot cover into the compartment;
There are a checklist “internal inspection – baggage compartment”, I made that checklist completed at this step;
In case the key is hard to pull out, push the compartment door then pull out the key
Electrical Systems
- Beacon – ON
- Alternator – oFF
- Fuel pump – oFF
- Main switch – On
If the battery is flat, the Beacon may not be illuminated – check MEL (Minimum Equipment List) ;
Make sure no circuit brake is pop-out - Fuel gauge – check again to see if there are any big different!
- Flaps – Up
- Nav light – On
- Strobe light – On
- Pitot heat – On
- LDG light – On
- Taxi light – On
(P.s More simply way to remember is that – excluding the “FUEL PUMP” and “TURN COORD”, turn On the five upper switch-breakers, SB )
- L.H Wing – Side
L.H.S Nav Light – Red;
Strobe light - L.H Wing – leading edge
Stall warning device – remember check!
Pitot heat – according to the training manual, we should not touch that because it is quite hot. However, instructor may tell you to do so, his/her consideration is that is warm at the starting. - Front – check Beacon and Nav
- R.H.S Wing
I remember that I was doing the pre-flight check at one day while an aircraft parked next to mine was started already. I kept attention to its movement while I kept myself away from the front of its propeller – it is simply to be understand: propeller drives air from the front to the rear of the aircraft. - Empennage – NaV light, beacon and the light on the Tail cone.
- Nav light – oFF
- Strobe – oFF
- Pitot heat – oFF
- Taxi light – oFF
- Instrument light – oFF
- Main switch – oFF
Well, it was time invite my instructor on board the aircraft. There were few items that I did before I went through the further checklist:
- Put the Hi-Vis vest oFF
- Adjust my Seat – height (by adding cushion) and fore-or-aft (by pull the latch under the seat) and inclination (by a knob on the R.H.S of the seat)
- Connect my headset to the socket on the center pedestal
- Fasten my seat belt
- Request Start up approval (in case circuit training)
As there are limitation on the number of A/C in the circuit, my instructor helped me request the start up approval at the last flight – circuit training – “Parafield Gound, TB10, YTN, request startup for circuit training”
Pre start checklist
- Maintenance Release (MR) – onboard and completed
- MEL – onboard
- Flight Manual (FM) – onboard
(MEL and FM are placed at the pocket or rank on the L.H.S seat.) - ATIS
Rightly, I needed to turn ON the Avionic Master switch;
Confirm the frequency on the COM2 STBY is 120.9;
Switch the COM2 “STBY” to “USE”;
Press the COM2 SPEAKER;
Remember switch ATIS from “USE” to “STBY” after receive the ATIS - Radio setting
COM1 – Ground 119.9 and Tower 118.7
COM2 – OPS 119.1 and ATIS 120.9
The latest frequency can be checked from ERSA (En Route Supplement Australian) and FTA intranet;
remember turn the Avionic Master Switch oFF - Nav setting
at this stage of training, I have not used that yet - Annunciator Panel
press the “TEST” – all light on that stripe should be illuminating;
Remember turn the Main switch oFF – prevent flat battery - Transponder
squawk 3000 – reference to VFRG and FTA document – in Class D Control Aerodrome;
remember the little knob is pointing “SBY” mode - Assigned Altitude Indicator
- Departure Brief – CTWO +
- PAX Brief
- Main Switch – On
- Cockpit light – two lights are at the upper of the cockpit – rotate to turn it on/oFF
Day VFR usually check if it works - Circuit Braker – all in – no pop out
- Fuel tank – select the lowest one – NO need to use the fuel pump – usually LEFT tank;
some fuel gauge may be not sensitive enough – just flip the fuel gauge few times – the reading should be back to previous reading (in the pre-flight check) - Mixture – full RICH
- Pitch – full FINE
- Carby Heat – Cold – most forward
- Flaps – up already;
if the indicator of the flaps status is not sensitive – flip the indicator few times - Nav light – On
- Autopilot Master – oFF
- Avionics Master – oFF
- HSI – SLAVE
- Park Brake – oN
- Alternate Static – IN – meaning using normal air intake from the static port at the rear
- ELT – at LEVEL position – meaning that is armed
- Oil temperature
Green range – hot prime – only need one priming;
Yellow range – cold prime – need three to four priming - Priming
confirm Throttle at the most aft-ward position;
fuel pump – oN;
move the throttle from most aft-ward to forward and back to most aft-ward – this is one priming; - Throttle – set
- fuel pump – oFF
(Fuel pump oFF AFTER the throttle is set!) - “Clear Prop”
check and clear the surrounding;
speak out loudly – “CLEAR PROP” – in order to warn others nearby
It’s time to crank the magneto – there are three things needed to remember:
- starting is followed by after start check – no much time to think!
- Close the door (or at least hold the door) – otherwise the strong slipstream may blow the door upward
- Push and turn the key
Most of us can say that we need to turn the key in order to crank the magneto, but I did not know that the skills – push and turn. Interesting! Practice is always essential in our learning.
After Start Checklist
- RPM check
not too slow or too too high – 1,000 to 1,200 rpm is our desire value;
remember that anytime once we stop or hold at a point, make sure the rpm at 1,000 -1,2000;
If the rpm is too slow, the “ALT” light on the advisory panel will be illuminating – this is not good for the engine – too slow rpm means that the Alternator will not be running, then the A/C will start to drive the power from the battery. - Oil pressure check
if the oil pressure is not going upward to green range – do the idle cut-off - Alternator – oN
- Voltmeter – Green range
once the alternator is turned oN, the voltmeter reading should be within the green range within seconds - Taxi LGT – oN
- TURN COORD – oN
- Autopilot pilot Master – oN – but in this stage of training – I kept it at oFF position
- Avionics Master – oN
“How do you read?” – “read 5”;
at some flights, the conversion is chopped – I needed to turn the knob on the center panel – tune the “squelch” - Suction gauge – green range
In most the past 10 flights, the reading is merely touch the upper green range – approx. 4.4 inHg - Navaids – at this stage of learning, I don’t need to do anything related to this item
Request Taxi
- Make sure it is using the “Parafield Ground” (119.9) on the COM1
- Wait for few second – ensure nobody is making a call – do not interrupt or jam the frequency
- Press the PTK (Push-to-Talk) BTN, wait – 1, 2, then – “Parafield Ground, TB-10, YTN, Dual, Base of Tower, Received Information F, For western training area, request taxing”
- Readback – “Run-up bay J, YTN”
In YPPF, there are 3 run-up bay: F, B, J – F is usually allocated for those A/C to join the circuit while B and J may be used for those A/C to take off at 03L/21R. Of coz, I needed to listen to the ATC instruction carefully.
Making a radio call is interesting at the first time, however, there are many things should be noticed:
- Say the service(frequency) name at the first time contact – e.g Parafield Gound, Parafield Tower
- Once the connection is established, we can only need to say our Call Sign at the first (OR say our call sign at the end in case of readback)
Taxi
- Depress the toe brake – the upper part of the pedal
- Turn the Park brake oFF – and release the toe brake
- move the throttle forward – small and smooth movement
- Once the A/C start to move – reduce the power a little bit
- Test the Left brake
- Test the Right brake
(P.s Do not need to stop the aircraft, only need to feel the brake is working)
Remember to clear both left and right in every turning;
Rightly, I stopped the A/C when I turn from parking area to the taxiway;
Also, I kept the A/C at the walking pace;
At the first time, I applied the toe brake while I wanted to use the rudder – so I learned that – Do not use the power against brake – keep the heel on the ground
Run-up bay
- Park into wind
follow the pattern OR determine the direction by checking the windsock;
remember remain enough space for taxi out the run-up bay - Balance the rudder pedal
if not, just apply some power in order to move forward a little bit and make both side of rudder pedal are balanced. - Park brake – oN
Give some pressure (Depress) on the toe brake, then Turn the knob to the Right (in case of TB10) - Switch tank
Fuel pump – oN;
Switch tank;
ADF – switch to “ET” mode and “RST” (reset) the timer
Fuel pump – oFF - Clear back – prevent no people will be hurt due to the prop stream
- Give some pressure (Depress) on the toe brake despite of using parking brake
- Move the throttle (smooth and slow) to 2,000 rpm
- Pitch check
move the pitch lever smoothly from full forward (FINE) to full backward;
once the RPM dropping, back to full forward immediately
(do this twice; and the max. allowable drop is 500 RPM – no drop more than 500 RPM) - Carby heat test
move the carby heat from full forward (cold) to full backward (hot) – the RPM drop is expected at least 30 RPM - Suction gauge – should be within the green range
- Magneto check
BOTH to LEFT – “tat-tat” , RPM should drop – then “tat-tat” back to BOTH
BOTH to RIGHT – “tat”, RPM should drop – then “tat” back to BOTH
(Neither side of magneto is allowed to have a reading that drops more than 175 rpm; and the difference in RPM drop between magnetos must be less than 50 RPM) - Throttle – idle – full backward
RPM drop and the reading is expected between 600-800 RPM while the “ALT” light on the advisory panel should be turned on;
remember move the throttle forward to achieve at least 1,000 rpm
In the 10 training lessons, I did the pre T/O check at the run bay as well
- Fuel – confirm selected
- Trim – Take off position
- Mixture – full RICH (full forward)
- Pitch – full FINE (full forward)
- Flaps – 10 deg flaps
if the indicator is not sensitive, try to flip the flaps indicator - Fuel pump – oN
- Autopilot – at this stage of learning, I do not need it – remain oFF
- Controls – “full and free” test by the combination of side-to-side and aft-and-fore movement of the control wheel – “full LEFT, full BACK, full RIGHT, full FORWARD, Neutral”
- Instrument
ASI – there is a knob to set the scale to show the TAS, but I don’t need to do so at this stage of learning;
Attitude indicator – make sure the miniature A/C is same level with the horizon bar, half blue and half brown;
ALT – turn the knob to the current pressure reference datum – in millibars (mb)
TC – wing level and ball center (balance)
HSI – turn the Heading Bug to the T/O direction – example in YPPF: RWY 03 – turn to 020 / RWY 21 – turn to 200;
Course bar to the T/O direction as well
VSI – read zero (0) - TCAD – turn it ON – it needs few second for warm up, then press the two button simultaneously – to the “G” (Ground mode)
- Clearance – I did not receive the clearance at this step
- TOSB – emergency situation during T/O rolling and at the transition of climb
“YTN, request further taxing” – as I made conversion and established the communication with the Ground, so I only needed to say my Call sign and intention.
After I received the approval about further taxing to holding point, I did the readback procedure and then started to taxi again. Once I arrived the assigned holding point– turn oN the parking brake.
I switched the COM 1 frequency to 118.7 (in case going outside to West TRA) / 124.6 (in case going for circuit training) while I set the “STBY” frequency to 130.45 (ADL CENTER) in case that I was going to departure for Western TRA.
“Parafield tower, TB10, YTN, ready for RWY 21R, for SKI departure”
Usually, you may expect two format of reply:
- Line-up
- In this case, I replied “Lining up, YTN”
- Transponder – “ALT” mode
- Strobe light – oN
- Pitot heat – oN
(P.s There is a “NAV LIGHT” between the “STROBE LIGHT” and “PITOT HEAT”) - Park brake – oFF
- ………. Taxi ………..
- Align the RWY center line
Usually, I received the clearance after I aligned the RWY - “Clear for T/O RWY 21R, YTN”
- LDG light – oN
(P.s LDG light is turned oN AFTER I obtained the T/O clearance – all SB is oN position)
- Clear for T/O
this case is more simply:-- “Clear for T/O RWY 21R, YTN” – do the read back procedure
- Transponder – “ALT” mode
- Strobe light- oN
- Pitot heat – oN
- LDG light – oN
(P.s “tat-tat-tat” – only need to press the remain the SB is oN – all SB is oN position) - Park brake – oFF
- ………. Taxi ………..
- Align the RWY center line
Take-oFF
- take a look at the windsock
- RIGHT HAND on Throttle ALWAYS!!!
- full Throttle + Right Rudder
(move the throttle smoothly – 1, 2, 3) - fast check T’s and P’s
- Lookout – look further away
- Airspeed
- Lookout – A.S – Look out – A.S
(P.s at this moment, the control wheel should be backward a little bit) - 65 KT – rotate
- Lookout- Attitude
(P.s DO NOT set a too high angle!) - Hold – A.S 80KT – Trim
(P.s DO NOT trace the performance…LOOKOUT…SET ATTITUDE~) - Lookout-Attitude
(P.s some instructors told their student to look back the RWY) - Lookout-Attitude-Performance (ALT, ASI, HSI)
This time should be climbing to 200′ (AMSL – in case YPPF) - Brake
- Flaps up
(pay more attention to look outside when the flaps is retracting – make some correction in backward pressure if necessary) - POWER – confirm set
- Lookout-Attitude-Hold-Retrim
(Ya…every thing was happening very fast) - Lookout-Attitude-Performance (ALT, ASI)
- before 500′ (around 45x’) – LOOKOUT – clear no threat
- 500′ – climb turn (or keep climbing)
- “A-L-A-P” cycle
- before 1,000′ (around 95x’) – level off – A-P-T
A – Push the nose down – set Attitude;
Wait speed until 95KT;
P – Reduce power to 23″/2,300 RPM (or 24″/2,400 RPM)
(Reduce Throttle before Pitch lever!)
T – Trim - LDG light – oFF
- Fuel Pump – oFF
My instructor sometimes asked me if I could identified where is the Bolivar Strobe light – they needed to us to understand that the A/C should remain south-west of the beacon in order to remain outside the Edinburgh Military Controlled Airspace while it should below 1,000′ – the reason is that there are inbound traffic at 1,500′. Keeping on the track of 325 DEG M to St Kilda (SKI).
Once passed the SKI, there are 4 things:
- Transponder – to 1200
- change to “SBY” mode
- squawk “1200”
- change to “ALT” mode
- COM1 change frequency – 118.7 (Parafield Tower) to 130.45 (ADL Center)
- Allow climb to below 2,500′
- Tracking the HSI HDG 325 DEG – Lookout should be to the mountain
(DO NOT use “Port wakefield road” as a reference – because part of the road is within the restriction area)
Once passed the Buckland Park Weather Radar, I am allowed to fly below 4,500′
During En route – I kept to do the “ALAP” cycle – Attitude-Lookout-Attitude-Performance
Also, I always report traffic, my instructor suggestion is that I only need to report any traffic with the converging flight path in clock code method.
After we arrived Dublin, my instructor would start the maneuver training. All the air exercise was using the DDM method – Demonstrate – Direct – Monitor
OK…let me skip the maneuver at this moment….however, it needed approx. 30 mins flying time to there, once I did few maneuver, I needed to fly at straight and level before the “FREDA” check:
F- Fuel – fuel pump oN, change fuel tank, fuel pump oFF, reset timer
R- Radio
E- Engine – T’ and P’
D- Directional Indicator
A- Altimeter
……….. Training ……….
Going back to YPPF – Locate a mast (or a little tower) called AERIAL FARM, then keep it on the left and fly to the sea (Gulf St Vincent). Meanwhile, I started to descend to 1,500′. After flying until little offshore, change the direction to the Outer Harbor (set the HSI HDG bug and CRS bar to 145 DEG)
………. “ALAP” cycle – Attitude-Lookout-Attitude-Performance ………
During En Route, I passed a place named Middle Breach where there is a village with many houses, so it was not hard to be identified. As I was flying from Middle Breach to the Outer Harbor. There is a danger area (D280) with height limitation – Therefore, I flew below 2,500′ (remain 1,500′) by Middle Breach.
I usually received the ATIS at this moment.
Pre Approach
- Compass
- Altimeter – set the pressure reference datum
- Aids – HSI (HDG bug and CRS bar to RWY direction)
- Mixture – full RICH
- Radio – set the COM1 “STBY” frequency to 119.9 (Parafield Ground)
- Approach Brief
“Parafield Tower, YTN, TB10, Outer Harbor, 1,500′, received information G, Inbound”
There were various method to join the circuit for landing. I may share later. After I (or my instructor) did the readback procedure. We did the pre landing check.
Pre Landing
- Brake – confirm park brake oFF and apply brake
- Undercarriage – I was only speaking out in order to cultivate the sense – I need to lower the LDG Gear if it is retractable
- Mixture – full RICH – confirm again
- Fuel – select the fullest tank – fuel pump oN, swtich tank
- LDG light – oN
- Seat belt – fasten
Sometimes, the tower may tell us about the traffic – e.g “follow TB-10, Number 2 for landing”, then I only need to reply “Traffic in sight, YTN”
When I joined the downwind (or during approch in case join base leg) – I (or my instructor) reduced the power setting to 23″/2,300 RPM
I usually received the “clear visual approach” clearance by the late-downwind (or just before joining base leg), I said – “Clear visual approach for RWY 03L / RWY 21R, YTN” – also, my instructors always turn the TCAD oFF at that moment.
I (or my instructor) kept the middle of blue stripe on the desire RWY
The A/C joined the Base leg directly OR once the wing was passed the threshold and little further forward – the A/C was starting to turn base leg – NOT over 30 deg AoB (angle of Bank)
- reduce the power setting to 10″/2,300 RPM
- Backward pressure – but maintain altitude 1,000′ – not descend yet
- once the speed within white arc – “white arc speed checked”
- lower 1st stage of flaps
- Start to descend at approx. 500 f.p.m – set attitude, hold, trim
(DO NOT descend below 600′ before turn to final)
The best height where the A/C starting to turn to final is at 750′
Final approach – NOT over 30 deg AoB (angle of Bank)
- Pitch – full FINE
- Undercarriage – DOWN and FIXED
- Flaps – FULL
- Reduce speed to 75 KT
- A-A-A
A – Aiming point
A – Aspect – keep the aiming point at 1/3 of the windshield, also the end of the runway should have same distance to the horizon
A – Airspeed – 75KT - Power + Pitch = Performance
I do remember that I needed to make the nose fly to the aiming point – it was scaring at the first time because I had the illusion and fear to crash the A/C. Yet, after few times trying, I learned that it is normal to maintain the nose pointing to the aiming point until the piano key disappear, retard throttle to idle and flare the aircraft. Flare should be smooth rather than abrupt movement – just maintain the backward pressure (more back than neutral)
Once landed on the RWY, I release the backward pressure, and I used the rudder pedal to maintain straight rolling while I applied the brake in order to slow the A/C. Then I cleared the RWY as soon as possible. Usually, I could stop the A/C for after LDG checklist and then made the radio call. However, I did these two procedure at the last time since the taxiway was not paved (sandy) – anyway – the after landing checklist is same:-
- Flaps – UP – stage by stage (2 stages)
- Fuel pump – oFF
- Strobe light – oFF
- Pitot heat – oFF
- Landing light – oFF
(P.s Only need to turn oFF 4 upper SB, switch breaker – there is 1 SB between each anothers) - Transponder – “SBY” mode
- TCAD – oFF already
So I can say the after landing checklist has 7 items but 3 things only ~
“Parafield Ground, YTN, TB10, on B2, taxi to FTA apron”
Oh yea, remember to switch back to Parafield Gound frequency (119.9) and confirm that there is no other transmitting signal before you make a call. Also, you need to say the frequency name at the starting (I do remember this now!)
……. Taxi …….
Shutdown
- Rudder pedal – balance (same level)
- Park brake – oN
- “TAXI LIGHT” – oFF
- “TURN COORD” – oFF
- Autopilot Master – should be oFF already at this stage of learning
- Avionics Master – oFF
- Magneto – “live check” and “dead check”
- Mixture – idle cut-oFF
- “NAV LIGHT” – oFF
- Alternator – oFF
- Main Switch – oFF
- Magneto – oFF
Cool! – I said (Good~ sometimes my instructor said). The first thing we did – opening the door! It’s hot inside the cockpit.
Vacating Aircraft
- fill the MR – “LOGBOOK TIME” and “AIRSWITCH TIME”
- Install the CONTROL LOCK
- Confirm Magneto oFF
- Confirm Main Switch oFF
- Wear the Hi-Vis Vest
- Pitot tube cover – oN
- Static port cover – oN
- Tie down and add the lock on the tail tie down hole
Cool la la ~ It was time to go back to the tower.
Finally, I finish this diary (sharing). Well, if you have read any misconception or incorrect knowledge, I do beg you to share (tell ,teach) me. Of coz, welcome to share yours with me at : tommy@tommykwan.com
(ver. 2016/04/12)